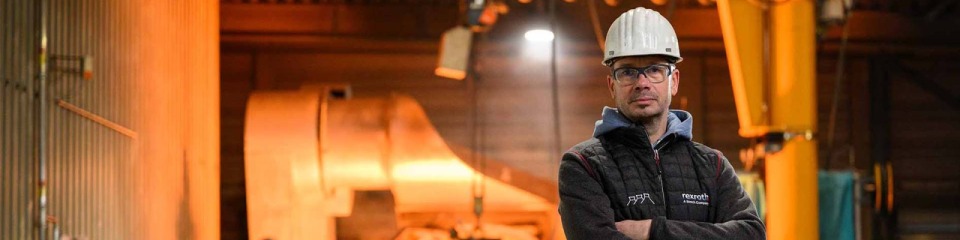
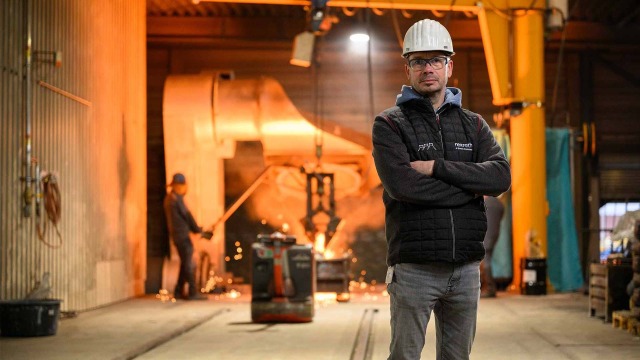
Select your location
Bosch Rexroth around the world
Asia & Pacific
Europe
At Bosch Rexroth, we’re constantly looking for ways to save energy. Discover some of the recent innovations we’ve implemented in our plants around the world – demonstrating how, with creative thinking and careful analysis, it’s possible to contribute to increased energy efficiency.
New ways to cool down
In the Lohr plant in Germany, hydraulic castings are produced in several different grades of cast iron. One part of this production process involves a special heat treatment called “annealing”, where the castings are heated to over 900°C, then cooled down according to precisely defined specifications.
An enormous amount of energy is used in annealing, but recently our experts have found a more energy efficient way – replacing annealing from the process by slow down cooling.
Our new cooling house enables us to eliminate the annealing process, helping us reduce the carbon dioxide emissions of our foundry by more than 2,500 tons per year. This has a direct impact on the Carbon Footprint of our products.
(Image right: Bosch Rexroth)
Reducing energy usage by modernizing the melting process
We have also installed our third new medium-frequency melting furnace at our Lohr foundry. The new furnace boasts state-of-the-art melting technology, where everything is designed for increased energy efficiency. This enables to replace three existing ovens by this new one.
By digitizing and automating the melting processes, restructuring the flow of materials and reducing the transportation of iron – and therefore the resulting temperature loss – we’re further reducing our energy usage. The new setup in our melting shop enables us to save up to 2.9 GWh of electrical energy per year.
(Image right: Bosch Rexroth)
Switching to central water cooling
Compression refrigeration systems are a key part of our Beijing plant’s hydraulic components production process. These operate in a similar way to refrigerators or air conditioners, with warm air emitted as the system runs. The warm air needs to be removed via the ventilation system, meaning a high energy consumption.
Our team looked at how they could improve their energy management, and turned to the existing cold-water network of the plant, which is already used to cool other machines and processes in production. They found that the energy efficiency could be significantly improved by using this existing cold-water network to cool installed machine tools. The compression refrigeration systems could be replaced by a heat exchanger connected to the cold water network.
We rolled this out in the first phase, where five machining centers were converted, resulting in reduced energy consumption for cooling by over 80% compared to the decentralized solution – equivalent to annual savings of about 85,000 kWh.
(Image right: Bosch Rexroth)
Circuit board production: saving energy with UV radiation
At the circuit board production facility in our Xi'an plant, China, synthetic resins are now being cured without heat by using UV rays, significantly improving the plant’s energy saving capabilities.
During the production process, printed circuit boards (PCBs) are mechanically assembled with electronic components and soldered. After functional testing, the assembled printed circuit board (PCBA) is coated with a paint to protect the electronics from external environmental influences. This makes it fit for use in industrial applications.
Until recently, this coating was dried with temperatures of about 100°C for 15-20 minutes, before the PCBAs had to cool for two hours. But by using UV technology, the production team could cause a chemical reaction within seconds, saving over 80% per PCBs in energy use compared to the previous process and reducing the drying time by about 90%. Not only that, but the process allows a thicker coating of paint to be applied, which means higher protection and better quality of circuit boards they produce.
(Image right: Bosch Rexroth)
Leo Pototzky
Director, Operational Sustainability