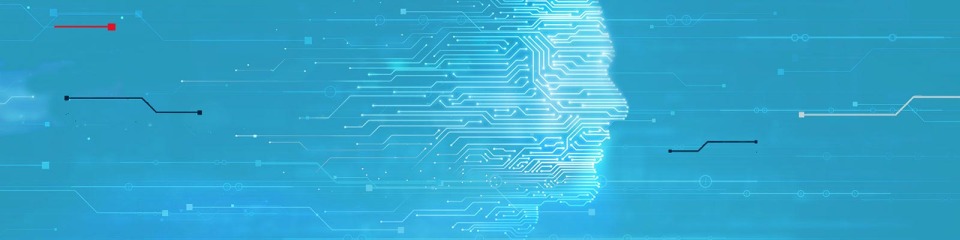
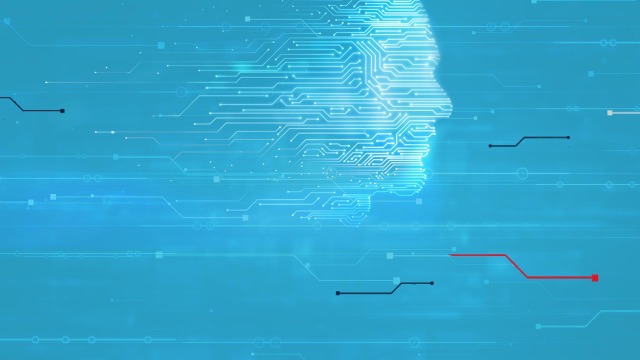
Select your location
Bosch Rexroth around the world
Asia & Pacific
Europe
In May, Professor Marco Huber told us about some of the exciting developments in artificial intelligence and what they mean for the manufacturing industry. If you want to benefit from AI but don’t know where to start, Marco Huber shares some useful recommendations in the second part of this two-part series.
Success in manufacturing AI is linked to developments in other areas, such as the Internet of Things, 5G, and blockchain. Could you tell us a little about the relationship between AI and these technologies – and maybe others, too?
The Internet of Things (IoT) is a necessity for the 24/7 deployment of AI solutions. The IoT allows data to be acquired from manufacturing machines and transmitted via the internet to the cloud or a server system. So the IoT is providing the fuel, while artificial intelligence is the engine. 5G will also play an important role, as it allows high-speed internet connection. It enables connectivity to be ramped up without significant investment in wired infrastructure. Furthermore, the low latency of 5G makes it an interesting technology where AI-driven decision making in real time is necessary, for example in controlling a fleet of AGVs.
In contrast, I don’t think blockchain/distributed ledger is as closely related to AI as the IoT, but it can become an important technology for data governance and data management, especially when combined with the IoT.
Another promising technology that’s closely related to artificial intelligence is quantum computing. Almost every machine learning algorithm basically solves a mathematical optimization problem, which is in many cases computationally very demanding. There’s huge potential for quantum computing to speed up optimization for many, but not for all, machine learning algorithms.
What advice would you give to manufacturers who want to benefit from artificial intelligence but aren’t sure where to start?
I recommend these four steps for getting started with artificial intelligence:
Firstly, start small, think big. To start with, work on individual process steps. Small advances will provide initial knowledge, insights, and confidence in AI, which in turn will strengthen your business case. With this experience under your belt, it’s possible to move on to bigger challenges.
Secondly, identify useful use cases early on. Use short development cycles in order to move forward quickly and to be able to act agilely and counteract difficulties if and when they occur. That way, you’ll get prototypes quickly.
Thirdly, pay attention to the benefits. Ultimately, whether an AI project succeeds or fails rests on this. It must offer the company added value. Let the technical department drive the topic forward and not necessarily the IT department.
My fourth tip is, take everyone with you. Don't forget the employees. If you can convince them of the benefits of an AI project, this will prevent unnecessary obstacles.
Can small and medium sized manufacturers benefit from artificial intelligence and, if so, how?
Yes, they can. As mentioned before, it’s becoming increasingly easy to implement an AI solution. By following the above four steps, it’s possible to benefit from AI. However, SMEs often have two major issues. Firstly, many SMEs struggle with the identification of relevant use cases. Secondly, people with sufficient time and skills are needed to realize an AI project. If either of these issues are present in an SME, I’d recommend looking for a partner, which can be a university, a research institution like Fraunhofer, or an AI service provider. At Fraunhofer IPA, we offer low-threshold project formats like the “Quick Checks” I mentioned in part 1. These formats are ideally suited to SMEs.
Artificial intelligence and the digital evolution as a whole rest on how well we can gain trust. How do you think we can build trust with OEMs and users?
A key ingredient to trust is transparency. This is unfortunately often lacking when it comes to artificial intelligence. As I mentioned in part 1, many machine learning algorithms behave like black boxes, but with techniques like explainable AI (xAI) it’s possible to provide insights. xAI allows bias to be detected in the data or the learned models, which might otherwise lead to inaccurate predictions or even discrimination.
How do you think artificial intelligence will complement, rather than replace, the human workforce in the future?
The famous quote by Steven Pinker still holds true when it comes to AI: “The hard problems are easy and the easy problems are hard.” Problems that are easy for humans, such as creativity, manipulation or perception, are very hard for AI. Other problems, like lifting heavy objects or calculations with large numbers, are hard for humans but easy for artificial systems. So there are many good reasons why humans and AI systems work well hand in hand. AI can take over the duties that are demanding for humans, which allows human workers to focus on higher quality jobs that benefit from the humans’ strengths. To achieve this, it’s necessary to consider a human-centered approach when developing AI systems. By that, I mean that AI systems should focus on people's needs, values, and well-being, thereby gaining trust and acceptance. In doing so, an AI system becomes operable for everyone: it perceives, understands, imitates and actively supports humans.
Professor Marco Huber is Deputy Director of the Institute of Industrial Manufacturing and Management (IFF) at the University of Stuttgart. He is also Head of the Center for Cyber Cognitive Intelligence (CCI) and Head of the Image and Signal Processing department, both at Fraunhofer IPA in Stuttgart. As a full professor for cognitive production systems, he manages and conducts R&D projects on artificial intelligence and machine learning applied to manufacturing, automation, and robotics.
The increasing availability of manufacturing data and advanced analysis tools is driving demand for data-driven approaches to improve the quality of workpieces and the efficiency of manufacturing processes.
At our plant in Homburg, we’re already working on different projects. Where valve housings for mobile applications are processed on a machine tool, we use data collected in the production cell in conjunction with machine learning methods to make near-real-time statements on the quality of the housing. Thanks to this solution, time-consuming downstream measurements in the laboratory are no longer necessary. The information on product quality enables the process parameters to be adjusted promptly, which reduces scrap and makes production more efficient and sustainable.
We’re also working on a research project that uses machine learning methods in conjunction with data from the hydraulic valve value chain to predict leakage results during end-of-line testing. Machine learning supports the continuous improvement process, reduces production costs by removing non-value-added production steps and ensures product quality.