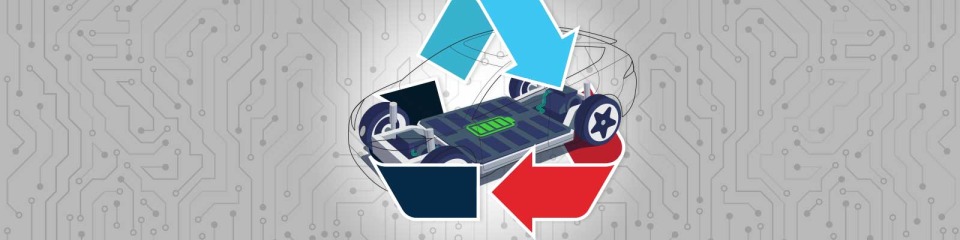
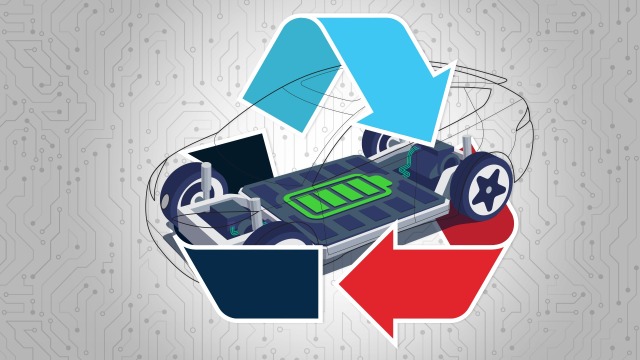
Select your location
Bosch Rexroth around the world
Asia & Pacific
Europe
The demand for electric vehicles is increasing. This raises a critical question: How can we obtain the raw materials and produce the required volume of batteries in an environmentally friendly and efficient way? The answer lies in battery recycling and automated solutions. Discover how we’re supporting the circular economy for electric vehicle batteries to help address this issue.
The move to electric vehicles is essential in the long-term battle to reduce CO₂ emissions and the use of fossil fuels. As a sector, road transport accounts for 16% of global CO₂ emissions1 and electric vehicles are a key component to decarbonizing road transport. Demand for electric vehicles is ever-increasing and it’s estimated that electric vehicles could make up about half of global car sales by 20352.
With a huge demand for electric vehicles comes an increase in demand for batteries – which requires automation solutions that will enable efficient, cost-effective, large-scale battery production. Bosch Rexroth is perfectly placed to meet this increased need with longstanding expertise in battery production processes. Flexible and innovative industrial automation solutions for battery production increase the efficiency and productivity along the entire value stream – from electrode and cell production to battery module and pack assembly, end-of-line testing and even recycling.
As the demand for the raw materials that go into producing these batteries increases, this in turn has environmental and cost implications. Raw materials, such as lithium, cobalt and nickel, account for a large part of the costs in the manufacturing of lithium-ion cells. But as up to 95% of a battery’s chemical elements can be recovered and recycled into the battery production process, it’s essential to also develop solutions that enable automated recycling of these batteries.
Steffen Haack
CEO of Bosch Rexroth
The circular economy – in which materials are re-used and waste is minimized – is a vital part of the drive to protect the environment. Experts estimate that global greenhouse gas emissions could be reduced by 39% by 2032 if global circularity is doubled3.
At Bosch Rexroth, we’re putting circular economy principles into practice by reintroducing valuable raw materials into the manufacturing process and reducing waste. We see this as an important part of our strategy to make our customers’ businesses and our own company more sustainable.
So it’s our mission to reinvent the circular economy for EV batteries. With our experience in EV battery manufacturing, we know how to assemble batteries, and therefore we know how to disassemble them with more efficiency and in an automated way.
Sebastian Krieger
Senior Manager Engineering and Sales Support Projects for Factory Automation at Bosch Rexroth
Only fully discharged batteries can be safely shredded and then broken down into their chemical components. So we’ve developed a complete automation solution for the deep discharging of batteries, which provides an introduction to industrial recycling with the potential for rapid scaling.
Our solution is made up of two Bosch Rexroth elements: the TS 5 transfer system and ctrlX AUTOMATION. The TS 5 transfer system transports batteries of different sizes and types from various manufacturers between the diagnostic discharging and dismantling stations. A modular solution from the automation toolkit ctrlX AUTOMATION then discharges the battery cells in the discharging station.
The discharging equipment automates the initial inspection, the deep discharging process with chemical inactivation and the final check. With this new system, a process that used to take 24 hours when it was done manually, now takes less than 15 minutes. It also improves safety for workers and significantly reduces the fire risk later down the line. This process will help to make battery recycling quicker, safer and more cost effective.
Sebastian Krieger
Senior Manager Engineering and Sales Support Projects for Factory Automation at Bosch Rexroth