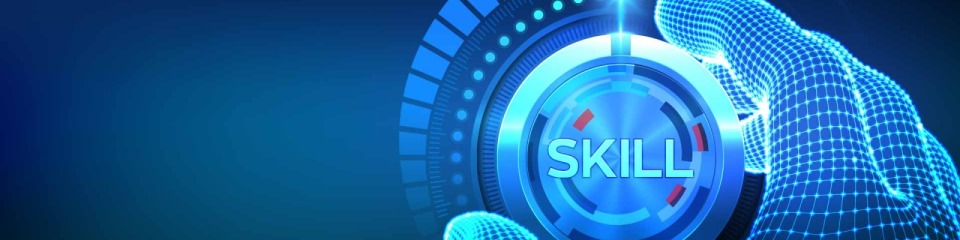
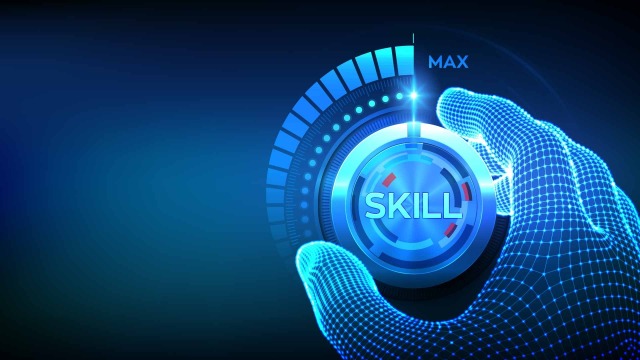
Select your location
Bosch Rexroth around the world
Asia & Pacific
Europe
If, like many manufacturers, you’re finding that acquiring skilled workers that can meet the challenges of the factory of the future is becoming a pressing concern for your business, help is at hand. Here we take a look at the circumstances surrounding the manufacturing skilled labor shortage and explain what we’re doing to help you counteract this issue.
With spending inching closer to pre-pandemic levels, many manufacturers are increasing their production volumes. However, uncertainties, such as the continuing disruption in the supply chain, volatility in energy and currency exchange, and the pandemic are, for many, proving to be problematic. The challenge of finding skilled workers, particularly in newer job areas, such as digitalization, is further exacerbating the issue. One report estimates that the global manufacturing labor shortage could exceed 7.9 million people by 2030, resulting in a potential revenue loss of $607.1 billion. Many countries now have aging populations and thousands of baby-boomers are reaching retirement every day. Not only is this resulting in the loss of highly skilled workers, but also the loss of their knowledge and experience. So, it’s more important than ever that manufacturing companies make themselves attractive as employers, both to encourage new people to work for them and to retain their existing staff.
Another major challenge that the manufacturing industry faces is the rapid pace of change where technology is concerned. The digitalized approach of Industry 4.0 and the factory of the future offers tremendous potential and opportunity for manufacturers to enhance flexibility and stability in their value streams, yet people are needed to implement, operate and manage this advanced digital technology. In fact, a whole new range of skills and expertise is needed from the manufacturing workforce – not just for the future, but for the here and now. Exciting opportunities are already opening up – in management, the analysis of big data, planning and decision making. On the factory floor, people are needed to operate, coordinate, oversee and work alongside connected machines. And, of course, all this machinery and technology needs to be maintained.
One of the ways manufacturers can counteract these issues is through the specific vocational training of employees. Providing vocational training opportunities to employees not only makes a business more attractive as an employer, it is also the only way for a company to keep pace with technological advancements, giving them a competitive advantage and enabling them to be more innovative and progressive.
Vocational educational systems are often slow to adapt to new technologies and job requirements, which is one of the reasons we set up our own training academy. The Bosch Rexroth Academy offers high quality training that increases competency and provides qualifications, ranging from basic knowledge to specialist technical training. We offer more than 100 different training courses in the fields of factory automation and the Internet of Things (IoT) / Industry 4.0, hydraulics for industrial and mobile applications, and pneumatics. Customer-specific training and selective technical training on site at the customer’s premises are available.
Our training programs are well-suited to a broad range of people, including young professionals looking for job specific content, specialists that need to deepen their knowledge in particular areas, service technicians, trainers and teachers that need to acquire specialist knowledge, and managers that need the right input in order to make responsible decisions.
As well as providing training to our industry customers, we also offer practice-oriented training in educational institutions worldwide, with training systems based on our products, technologies and manufacturing skills, to give learners real-life practical experience, as well as the supporting course materials.
Systematic and continuous learning enables your employees to stay up to date with the latest technologies and helps to give your business a competitive advantage, while also helping you to retain valuable staff. Although training does have a cost, in today’s highly competitive market, and with the skilled manufacturing labor shortage an ongoing issue, the cost of not providing training is far greater.