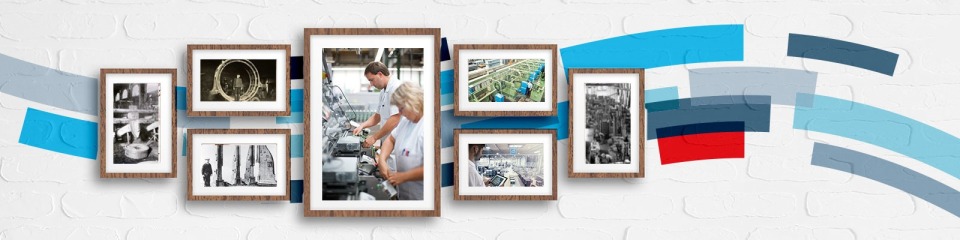
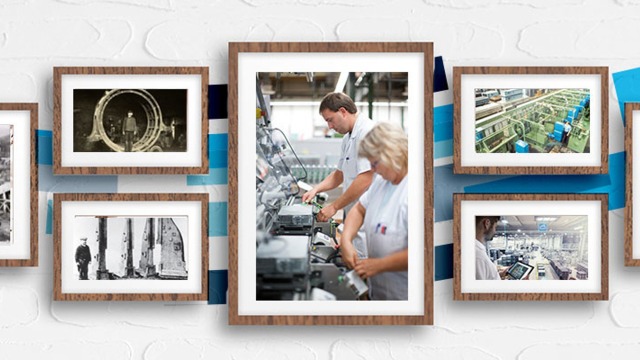
Select your location
Bosch Rexroth around the world
Asia & Pacific
Europe
From the hammer mills of the industrial revolution, to the first machine tools, to the factory of the future, here you can see at a glance how manufacturing and factories have changed over the years.
Water- and steam-powered hammer mills extracted the iron out of ore, satisfying the increasing demand for raw metal. Apart from the hammer movement, all the work was done manually using very simple tools. When Georg Ludwig Rexroth set up a water-powered hammer mill in the Spessart region of Germany over 225 years ago, it marked the starting point of what would eventually become Bosch Rexroth.
With the progress of industrialization, engineers needed more and bigger construction parts made of iron for machinery and construction. At the time, cast iron manufactured in foundries was considered to be state-of-the-art, but the working environment was extremely hot, dirty and dangerous.
One hundred and thirty years ago, Robert Bosch was using a pedal-powered workbench weighing 300 kilograms to make parts for the magneto, the product that marked Bosch’s breakthrough. Workbenches like this mark the transition from craftmanship to industrial manufacturing.
With the arrival of electricity in factory halls, the machines and systems became more efficient. Electric drive belts made their way into factories and enabled the first steps towards mass production, as shown here in the production of spark plugs at Bosch.
The introduction of the assembly line and the process-specific division of labor made high volume production more efficient, especially in the rapidly growing automotive industry. Following Ford's example, Bosch introduced assembly line production in 1925.
From the 1950s onwards, hydraulics enabled a breakthrough in mechanical and plant engineering. Its force density and robustness were ideal for high-performance presses, injection molding machines and die casting machines.
At the same time as the development of the first microchips, the first programmable logic controller for machines was invented. This enabled machines to execute program commands one after the other and automate work processes. The beginning of the electronification of mechanical engineering and manufacturing changed the way machines were operated.
By switching from manually operated individual machines to fully automated transfer lines, automobile manufacturers and suppliers such as Bosch greatly improved efficiency and quality in high-volume production. Bosch Rexroth paved the way for this progress with the development of the world`s first maintenance free AC-motors.
From the early 1980s, robots started to take on more and more physically demanding tasks in production, significantly increasing efficiency. At the same time, they improved reproducibility and thus quality in serial production.
In machines and systems, software was becoming increasingly important. One key advantage was that, rather than having to manually set up a machine for a product change, this could be done with just a few clicks of a mouse.
In order to stay competitive, more and more manufacturers are individualizing their products. This poses a challenge to the production department to realize variant-rich production. The Bosch Production System combines the advantages of human flexibility with highly efficient automation. Manual workstations are ergonomically and functionally adapted to the new requirements.
Industry 4.0 and the Industrial Internet of Things bring IT and automation together. People, machines and processes are networked, which significantly increases efficiency in large-scale production and enables very small quantities to be produced economically.
The direct collaboration between humans and robots without a safety fence relieves employees of strenuous and dangerous work. Production assistants with sensor skin detect the presence of people, ensuring safe operations. Artificial intelligence enables them to learn without programming.
3D printing opens up new possibilities in the design of lightweight components and individualized products. In combination with state-of-the-art automation, the technology is establishing itself as a strong addition to traditional manufacturing methods.
In the factory of the future, all production sites will be wirelessly networked and mobile. Production lines will be flexible and able to form independently to suit requirements from large series to batch size 1. Digital twins will enable the virtual optimization of all processes and make production more sustainable. Meanwhile, humans will still be at the heart of the factory, coordinating and controlling production.