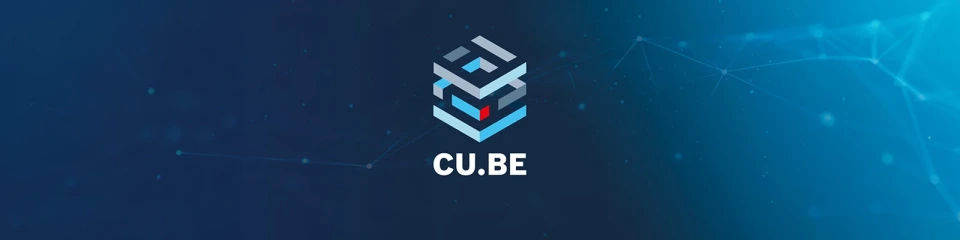
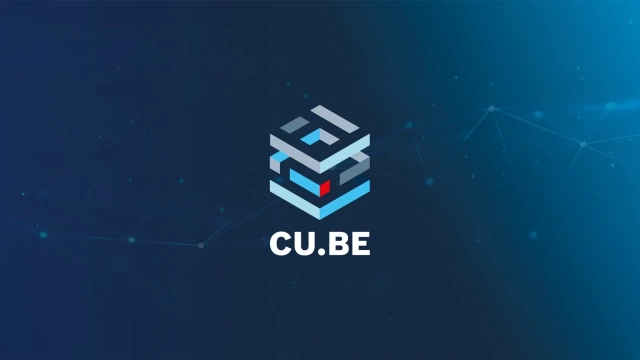
Select your location
Bosch Rexroth around the world
Asia & Pacific
Europe
Experience Innovation, Collaboration, and Customer Benefits
At the Bosch Rexroth CU.BEs, we combine our market expertise with a spirit of openness, creativity, and excellence to drive the future and deliver actionable results.
Discover the future at CU.BE and depart with results that fast-track your success.
Work with us to create the solutions you’d like to see. We’re inviting industry professionals, researchers, academics, innovators and opinion leaders to come to the Bosch Rexroth CU.BEs and experience the future.
Together, let's explore new directions of development, work together and seize opportunities, through innovation, collaboration and customer-centric solutions.