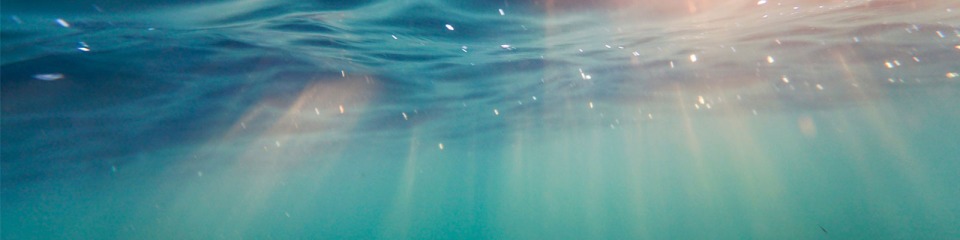
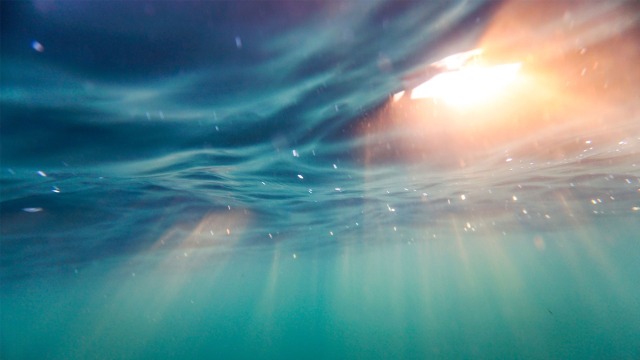
Select your location
Bosch Rexroth around the world
Asia & Pacific
Europe
Since our new disruptive innovation, the SVA R2 subsea valve actuator, won the prestigious Hermes Award at this year’s Hannover Messe, we’ve had lots of enthusiastic feedback from people around the world. Many of them want to know more about how we developed the world’s most compact electric subsea valve actuator. So we asked Dr. Alexandre Orth, Head of Subsea Automation Systems at Bosch Rexroth, to tell us all about it.
When did you first realize there was a requirement for this type of product?
At the start of 2019, I was visiting a leading subsea equipment builder for offshore energy production in Norway, with my colleague Tor Jensen. We asked them what their biggest technical challenge was, and they told us they needed an electric subsea actuator with a reliable safety system for the small bore valves. This surprised us, as we thought they already had a solution in place to complete the planned electrification of their current machinery. But they told us they couldn’t find or design a cost-effective electric actuator without compromising on size or safety.
We took on the challenge: to design an electric subsea actuator that can operate at sea depths up to 4,000 meters, safely and reliably, but without requiring any more space than the current hydraulic cylinders. At that time, it seemed like mission impossible, but we let our team look into it.
How do you go about developing a disruptive subsea innovation like this?
As part of the new business area, we could perform like a start-up inside Bosch Rexroth. It gave us an entrepreneurial mindset and the focus we needed. And, by using agile project methods, we could speed up this development, involving the whole team in a multi-technology design journey. The team itself was enhanced by the expertise of other Bosch divisions.
Additionally, by applying user experience methodology, we were able to confirm that the need for this type of product was there – not for just one customer but for all the main players in the market. Early prototypes enabled us to confirm the main requirements and to get customer feedback on the key features, which are critical for the standardization process.
Which are the main technical standards for subsea applications?
The SVA R2 is designed for any process industry below water. Looking at oil and gas production, it must meet strict international standards. Customers also have their own specific requirements regarding functions and testing procedures, besides our own high quality procedures. But, as what we’re doing is completely new, we also applied research – for example, in a PhD thesis, we aim to demonstrate that our mechatronic system can operate for 30 years subsea without preventive maintenance.
How long did it take to develop?
Roughly two years. That’s a very short time for such a complex automation system. It’s about twice the standard speed for this kind of product development. But, by getting constant feedback from different stakeholders, we’ve not only delivered the product swiftly, we’ve also created a standard product that‘s suitable for several use cases.
How many people were in the development team?
Around 10 people work full-time in our team. We also count on the support of colleagues in different parts of Bosch Rexroth worldwide, as well as the wider Bosch Group.
Did you work with other partners during the development process?
Of course, you can’t achieve groundbreaking subsea innovation alone. We collaborated with our clients, leading operators and machine builders in order to understand the real technical challenges. We then involved our suppliers and different areas of Bosch to help identify the best technological solutions to these challenges. And we work with universities to gather valuable research. Finally, with certification and classification societies, we can provide neutral third-party quality assessment, as requested by our stakeholders.
What did you enjoy most about this project?
Firstly, our innovative team spirit, which made the impossible, possible! Secondly, our multi-cultural collaboration with colleagues and clients worldwide. And thirdly, the high engagement from our external partners – a vital part of our agile team.
Were there any significant issues or challenges you had to overcome?
There were many technical challenges. For a start, we had to make a complete electric actuator the same size as a hydraulic cylinder, whilst keeping field-proven safety. Then, there were the challenges around the power supply – the actuator has to run with the power of a sensor with 24V DC. The maximum operating depth was increased from 3,000 meters to 4,000 meters to make it ready for future applications. And all the while, we had to keep manufacturing costs affordable, make the product energy efficient and integrate a safety function certified up to Safety Integrity Level 3.
Did the pandemic impact your work?
Absolutely. Working with an international team is challenging when you can’t travel. But mostly we miss the direct contact with our customers and getting face-to-face feedback. However, there are positive outcomes of the pandemic too, such as the digital trade show, Hannover Messe, which was easily accessible to people from all around the world.
What’s the most important customer benefit of the SVA R2?
Safety. The customer gets an automated system, operating far away at the bottom of the ocean, that is completely safe and reliable. Our system not only enables the safe electrification of subsea production systems, but it does this within the same space as a hydraulic cylinder, so it can be easily retrofitted in existing plants.
Can you tell us about the environmental benefits and why these are important?
For an innovation to be future-proof, it must be sustainable. Protecting the environment is important, not just to us, but also to our customers.
For decades, operators of subsea process plants have used hydraulic cylinders to open and close valves. To operate a hydraulic cylinder at a depth of 4,000 meters, you need several kilometers of hydraulic pipes and a large central hydraulic power unit above water to supply the valves with the necessary fluid power via these lines. This is very energy intensive. Thanks to our subsea actuator, the hydraulic system, the central power unit, the pipes and hydraulic controls aren’t needed. This eliminates the risk of control fluid leaking into the ocean and removes all the energy losses caused by the long hydraulic pipelines.
The low voltage that also supplies the sensors underwater is sufficient for the power supply of the electric subsea valve actuator. This saves operating costs and sustainably reduces the carbon footprint of subsea factories. The green credentials were an important part of why we won the Hermes Award for this subsea innovation at Hannover Messe this year.
Did the Hermes Award open new doors for you?
For sure. Until then, subsea technology like this was only known to a select group of customers who work in this field. Now many people and potential customers around the world are aware of our innovation. We’ve had interesting feedback from people in Japan, China, Australia, Africa, Brazil, Europe and the United States, which can only lead to further exciting developments.
Who will benefit most from the SVA R2?
First of all, the offshore oil and gas industry that provides us with vital energy. By enabling the electrification of its subsea production systems, we’re making it more sustainable. We’re also discussing how the SVA R2 can be used for carbon capture and subsea storage. This would drastically reduce the CO2. It can also be used to actuate valves for green hydrogen production offshore. And last, but not least, the SVA R2 can operate any kind of process valve, so there are applications in civil engineering for water management or even applications above water.
Have you received any customer feedback?
Yes, we have – and our customers have confirmed the disruptive potential of the SVA R2. They believe this is the missing link that will make the All Subsea Factory a reality soon.
When will the SVA R2 be available?
By the end of the year, customers will be able to get the first prototype to enjoy in their facility or as part of their subsea applications. We’ll also be presenting the SVA R2 at the Offshore Technology Conference in August, so visitors can come and see it for themselves and find out more about it.
Can you tell us anything about your next project?
The SVA R2 isn’t the end of subsea electrification, it’s just the beginning. We’ve already been asked to provide more smart solutions for other types and sizes of valves. We’re also looking at other ways to make the All Subsea Factory a reality, while dealing responsibly and sustainably with the world’s oceans.
In the medium term, we see considerable potential for use in the production of green hydrogen. Offshore wind energy plants can be used to economically produce large quantities of hydrogen CO2-free. Another application is carbon capture and storage plants, which stores CO2 under water in former production sites. We’re already in initial talks about this.
Alexandre Orth (right-hand side) with Gottfried Hendrix (System Engineering Manager).